»Mono Vest is part of a technical cycle, a closed loop system where all core feedstock is sourced locally from the same nylon family. The products are made in Germany and can be recycled later in an existing infrastructure.«
Prof. Friederike von Wedel-Parlow
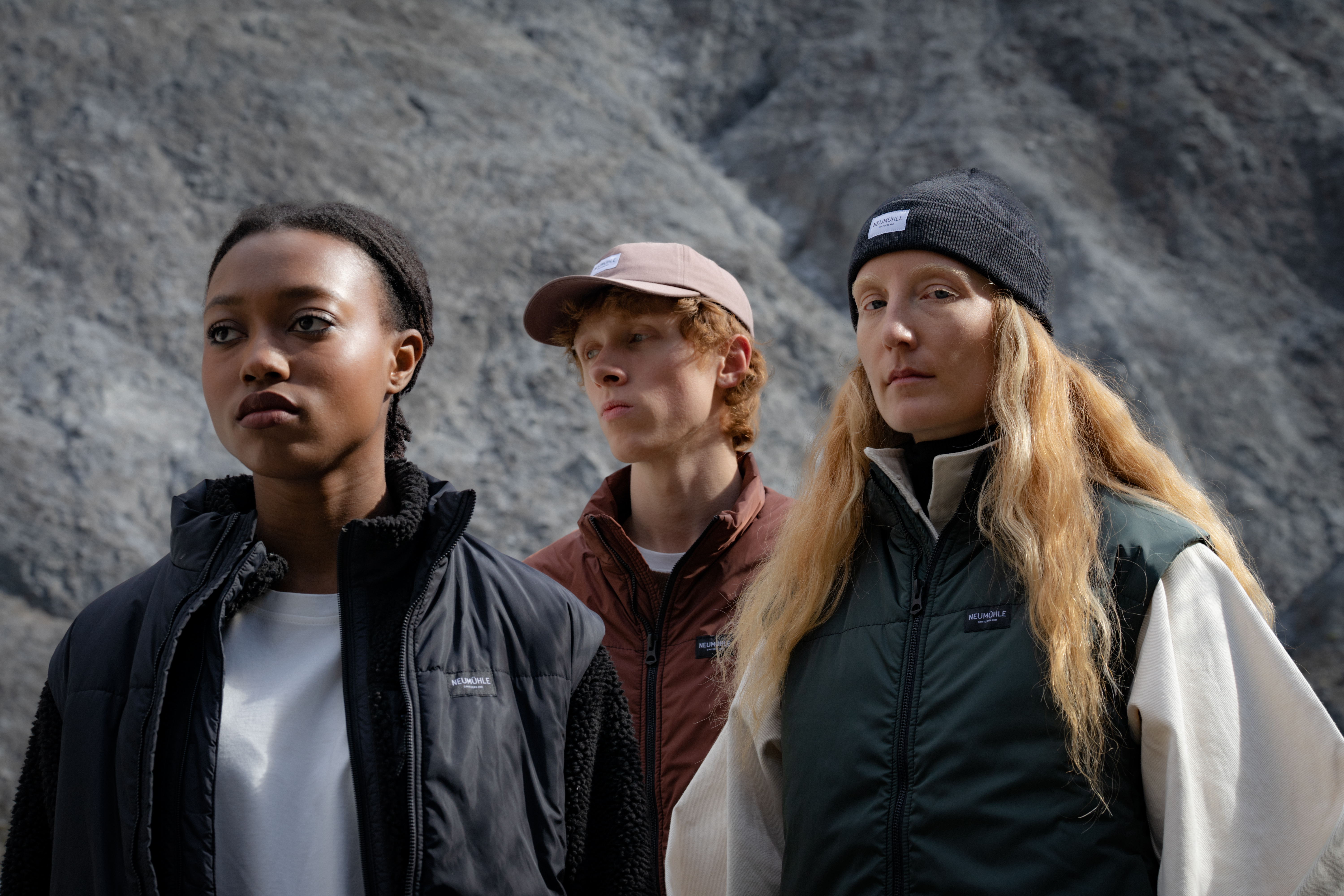
Three questions for Andreas Fehr, founder
How did the idea for Mono Vest – circular and local come about?
Fast fashion causes 10% of carbon emissions worldwide. A lorry-load of clothes is taken to a landfill site or incinerated every second. Our goal is to face this global problem locally. The original idea goes back to 2019. We wondered how we could develop future-proof clothing that could be reused as a resource without any loss in quality. We want to guarantee material flows that are circular. The Mono Vest allows us to pave the way for a radical circular economy. It’s underpinned by a local production chain in Europe and manufactured in Germany.
What was your personal highlight in the Mono Vest development process? Was there a low point?
The development process took three to four years. There were some highlights, but also challenges. It took ages to set up the supply chain, particularly since there are virtually no solutions for recycling textiles. One highlight was when the lab belonging to our recycling partner (ECONYL®) confirmed that the current 2023 Mono Vest version could be recycled. This was quite a breakthrough where circularity is concerned. We’re proud that we now have one of the first textile products that’s part of a closed loop in the real world.
Where do you see your project in the next five years?
We’ll be focusing on growing the collection and creating new products based on this expertise and the local, circular system. In the process, we want to apply our skills to new processes and developments because the route to a full circular economy is still very tricky. And we want to play a role in changing the textiles industry.
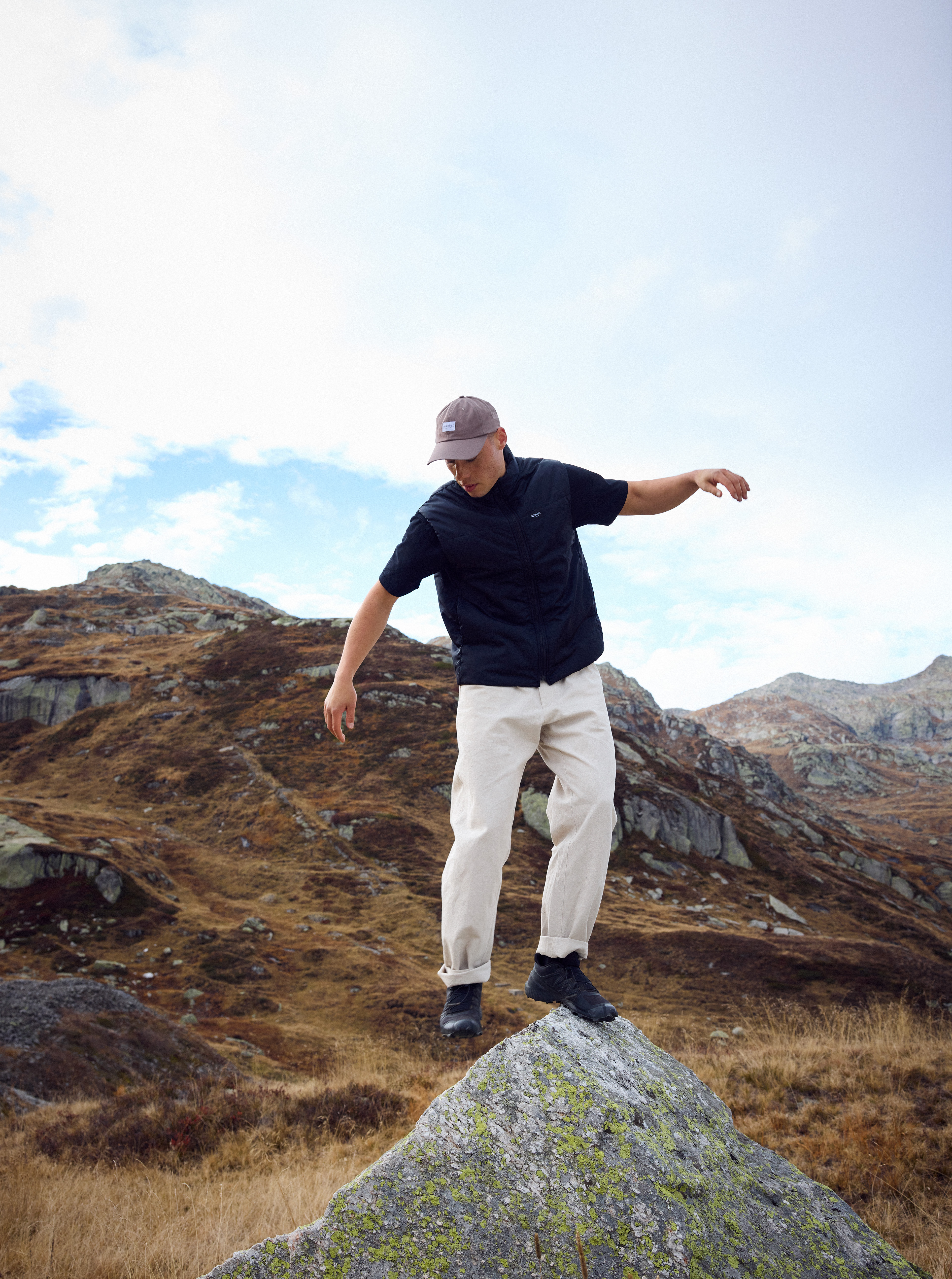